1. 서 론
세계적으로 미세먼지로 인한 대기오염 문제의 심각성이 대두되고 있다. 최근 보도에 따르면 ‘21년 미세먼지로 인한 대기오염 사망자가 450만 명으로 전년도에 비해 2배 늘었으며, 이로 인해 미세먼지 관련 질환에 대한 사회적 인식이 높아지고 있는 추세이다. 세계보건기구(WHO) 보고에 따르면 매년 미세먼지로 인해 전 세계의 평균 대기 오염농도(35μg/m3)가 배에 달하는 수준으로 증가되고 있으며, 한국의 경우 전국 평균 대기 오염농도가 18μg/m3인 곳에 살고 있다고 지적했다. 또한 실내가 충분히 환기되지 않으면 고립된 실내 공기질도 시간에 따라 점차 오염도가 증가될 수 있다. 따라서 창문을 통한 환기에 대해 실내 공기질 정화를 목적으로 국내 및 해외에서는 청정공기 관련 연구가 지속적으로 진행되고 있다.
현재 사용되고 있는 방진망은 유리섬유(Fiber glass)를 사용해 불에 잘 타지 않고 소수성 성질이 외부의 수분을 효과적으로 차단하며, 청소가 용이하며, 수명이 길다는 장점을 보유하고 있다. 그러나 입자크기가 매우 작은 미세먼지는 방진망 메시(Mesh) 사이사이로 통과되는 단점이 있다. 이를 보완하기 위해 미세먼지 방진망에 전기방사[1] 기술을 적용하여 작은 입자의 미세먼지까지 걸러낼 수 있는 방안을 Fig. 1.와 같이 PVDF(Poly vinylidene fluoride) 미세먼지 방진망을 제조해 가정과 공공시설 창문 등에 응용 가능성을 판단하려 한다.
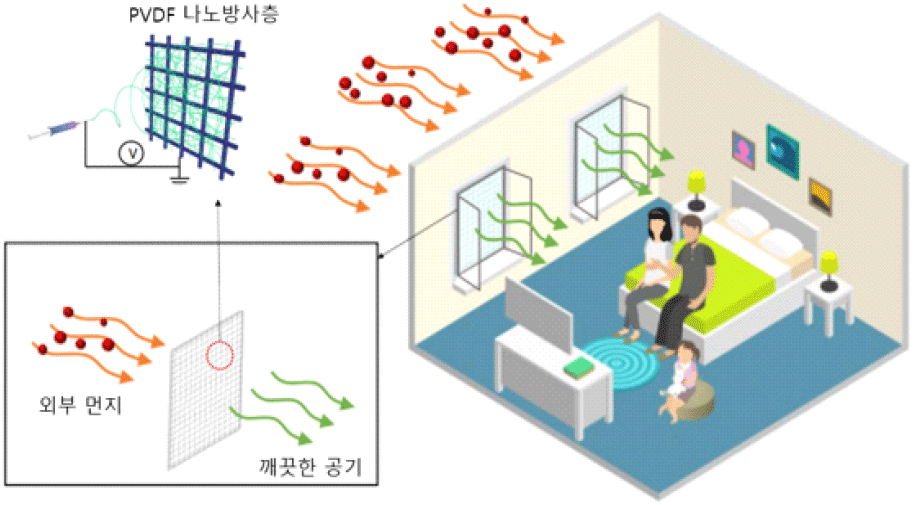
전기방사 기술은 니들팁 끝에 고전압을 주게 되면 고분자 용액의 방출로 인해 제트(Jet)가 형성되며, 날아가는 과정에서 용매가 증발해 나노섬유를 제조할 수 있는 공정이다. 비교적 간단한 구조와 저가의 장비를 이용한다는 장점이 있으나 전기방사 기초지식과 공정 및 기술적 매개변수들을 고려해야 하는 다소 복잡한 기술이다. 이러한 전기방사 기술을 적용해 용매가 용해 가능한 모든 고분자 재료로 나노섬유를 쉽게 포집할 수 있다.
실험에 앞서 관련 선행연구논문 검토 결과, Wen Liang[2]은 폴리우레탄(TPU)을 기반으로 전기방사 기술을 적용하여 얻은 나노섬유를 포집해 투명 공기필터를 제조하는 방식을 적용하였다. 해당 방식은 TPU와 높은 합성섬유의 높은 혼화성으로 인해 높은 미세먼지 차단 성능을 갖는 나노 방진망을 제조 가능하도록 하지만 PM10 및 보다 작은 미세 입자에 대한 차단 성능이 여전히 부족하며, 내구성이 약하다는 문제가 있어 이에 대한 개선이 필요한 상황이다.
따라서 본 연구에서는 TPU의 장점인 우수한 화학적, 열적 안정성을 가지며 여러 필터 또는 멤브레인에 널리 사용되는 PVDF 소재를 적용하여, 전기방사 기술의 다양한 매개변수와 작업환경에 따라 발생하는 문제점과 변수를 최소화하기 위한 방안을 모색하였다. 또한 전기방사를 위해 최적의 PVDF 용액 비율을 확인하고 나노섬유를 수집하여 만들어진 PVDF 전기방사 부직포의 표면 성질은 주사전자현미경을 이용하여 분석한다. 이로부터 만들어진 PVDF 미세먼지 방진망의 공기투과도와 분집포집율은 자동 여과 성능 시험기와 자동 필터 테스트기 장비를 이용하여 분석하여, 공기투과도와 분진포집율을 동시에 만족하는 것이 본 연구의 목표이다.
2. 전기방사 공정 중 다양한 매개변수의 영향
전기방사 실험은 다양한 매개변수[3,4]를 미세 조절하여 방사가 이루어지며, Fig. 2.와 같이 광범위하게 분류된다. 이러한 매개변수를 적절하게 조작하여 원하는 나노섬유의 형상과 직경을 얻을 수 있다.
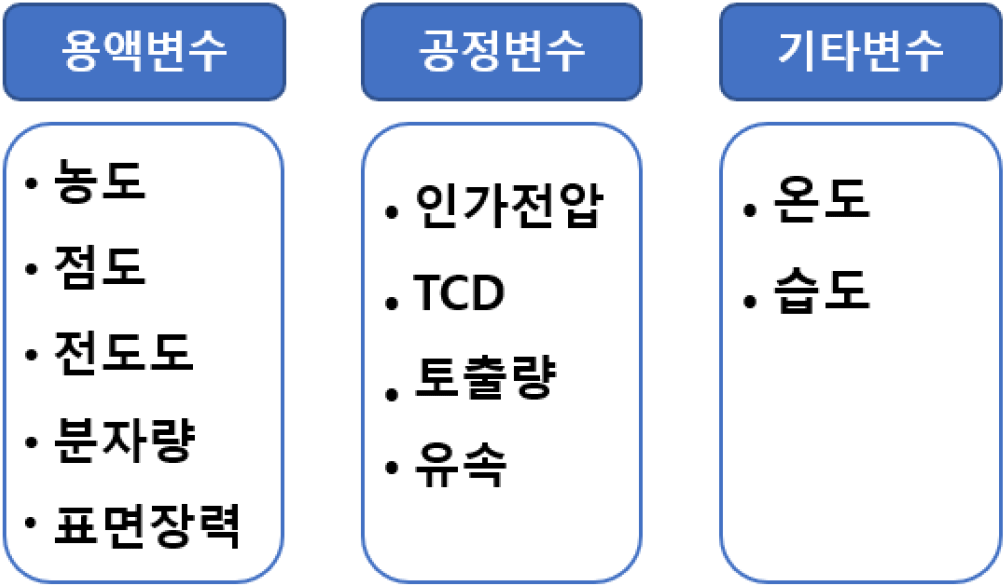
용액 매개변수에는 농도, 점도, 전도도, 분자량, 표면장력 등이 포함된다. 섬유 형성을 위해서는 최소한의 필요 용액 농도와 표면장력이 필요하며, 적절한 농도는 주사 팁 끝에 용액의 흐름 유지와 연속적인 섬유의 형태와 직경 및 비드(Bead)를 결정하는 데에 있어 매우 중요하다. 표면장력은 제트 형상과 섬유 형태 결정에 중요한 역할을 한다. 이는 사용하는 용매의 차이에 따라 표면장력의 차이도 변화를 나타난다. 표면장력이 낮으면 부드러운 섬유를 형성할 수 있으며, 높은 표면장력에서는 구슬 형태의 섬유를 형성할 수 있다. 따라서 사용하는 용매의 변화에 따라 섬유 형태의 변화를 조절할 수 있다.
섬유를 형성하는 데 있어, 공정 매개변수들도 중요한 요소이다. 공정 매개변수에는 인가전압, TCD, 토출량 또는 유속 등이 있다. 전기방사시 니들팁과 컬렉터 사이에 전압을 인가하면 니들팁에 형성된 방사 용액 방울 표면에 전하 또는 쌍극자 반발로 인해 테일러콘(Taylor Cone)이 형성된다. 이때 전기방사 매개변수에 따라 다양한 형상의 테일러 콘이 보이게 되는데 그 형태는 원뿔과 같이 관찰된다. 또한 인가전압에 의한 반발 정전기력이 표면장력을 극복하게 되면 테일러 콘 끝에서 제트를 띄며 접지된 쪽으로 방출되게 된다.
TCD는 니들팁과 컬렉터 사이의 거리로 니들팁으로부터 방출된 나노 섬유가 건조되는 구간으로 이때 섬유가 충분히 건조되어야 한다. 전기방사를 하는 대부분의 경우 결과적으로 균일한 직경의 섬유 생산을 목적으로 한다. 인가전압이 높거나 낮으면 용매의 증발하는 시간이 불규칙하며 섬유의 직경도 얇거나 두꺼워진다. 또한 방출되는 테일러 콘과 제트의 형상이 불안정하게 된다.
따라서 적절한 인가전압 조건 하에 전기방사 실험을 진행해야 하며, 용매가 적절히 증발해 안정적인 제트의 형상으로 컬렉터에 섬유가 수집되게 된다.
용액, 공정 매개변수 외에 기타 매개변수[5,6]로 온도와 습도가 존재한다. 방사를 진행할 때 주위의 온도, 습도는 섬유의 형태와 직경 및 비드에 큰 영향을 미친다.
온도에 따라 방출되는 용액의 증발 속도에 영향을 주어 온도는 평균 직경을 변화시키는 주요 요인으로 용매의 증발 속도와 용액의 점도는 평균 직경에 영향을 미치는 상반되는 메커니즘이다. 습도는 높을수록 수분 흡수 및 침전이 많이 발생하므로 생성되는 나노섬유 형태의 큰 영향을 준다.
본 실험에서는 실내 온도 23±3°C, 습도 35±5%를 일정하게 유지하였다.
3. 전기방사 실험
본 실험에서는 이소불화비닐(Polyvinylidene fluoride(PVDF), Mw = 534,000, Sigma-Aldrich), 다이메틸폼아마이드(N,N-Dimethylformamide(DMF), 99.0%, Samchun Pure Chemical Co., Ltd.),그리고 아세톤(Acetone, 99.5%, Samchun Pure Chemical Co., Ltd.)을 사용하여 전기방사 용액을 제조하였다. 전기방사 용액 제조에 있어 DMF는 용매를 녹이는 극성이 있어 전기방사 실험에 가장 많이 사용한다.
기본적으로 실험을 수행하기 위한 전기방사 장비[7]는 아래와 같이 고전압을 5kV~25kV까지 인가할 수 있는 전압 공급장치(High Voltage Power Supply, SHV300, NanoNC, korea), 토출량과 유속을 조절할 수 있는 실린지 펌프(Single Syringe Pump, NE-300, USA), 형성된 나노섬유를 수집할 수 있는 집전판(Collector), 노즐(Single Plastic Nozzle, NanoNC, korea)이 Fig. 3.과 같이 구성되어 있다.
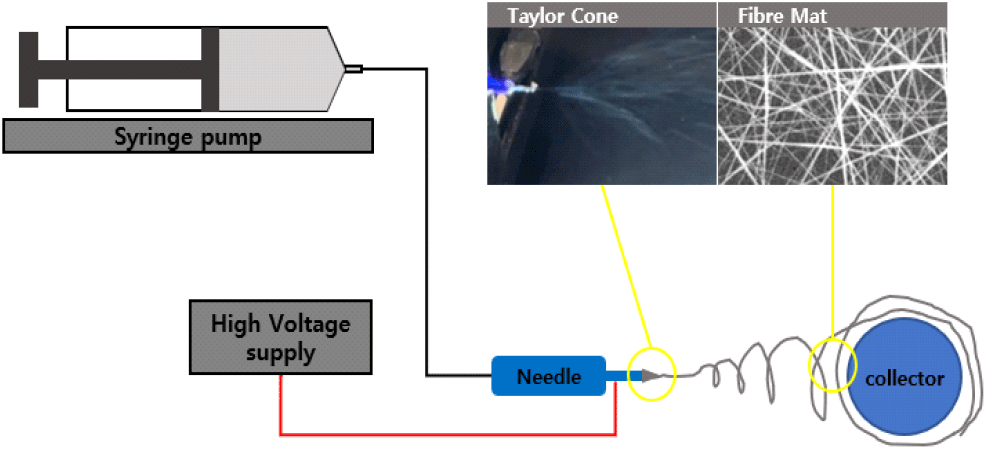
전기방사 실험을 수행하기 위한 용액 제조는 아래와 같이 진행하였다. 먼저, DMF와 Acetone을 각각 질량비 2:3, 1:1, 3:2 비율로 혼합하였다. 이후, 각각의 혼합 용제에 PVDF를 12, 15, 18wt% 농도로 첨가하여 12시간 디지털 가열식 자력교반기(HSD180)를 통해 교반하였다. 최종적으로는 Fig. 4.와 같이 PVDF Solution을 제조하였다.
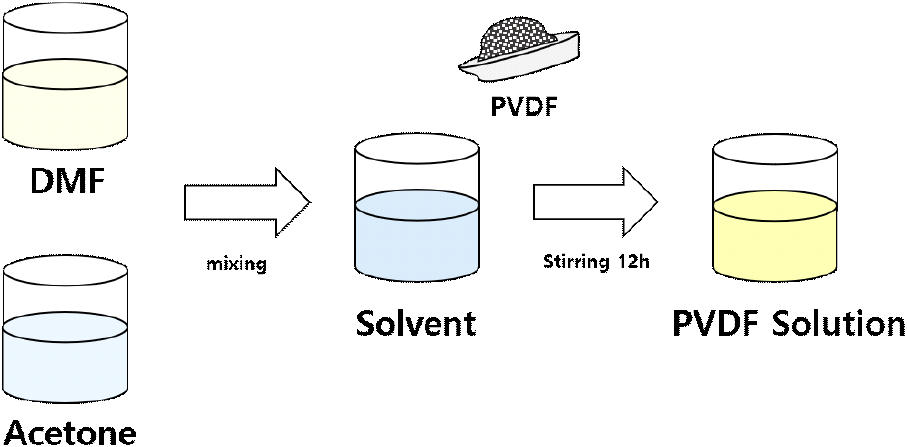
또한 전기방사 실험의 주요 매개변수는 아래와 같이 용액의 방출 속도(1.0 ~ 10.0ml/h,), TCD(15cm), 인가전압(10~20kV), 노즐의 직경(21G)로 설정하였다. 이러한 조건 하에 컬렉터 알루미늄 호일과 유리섬유 방진망을 감아 샘플에 일정 시간 동안 나노섬유를 수집하였다.
전기방사 공정을 거쳐 수집된 나노섬유 형태와 직경 및 비드를 확인하기 위해 전계방사형 주사전자현미경(JSM-7100F, FE-SEM)을 활용하여 부직포 표면을 세밀하게 관찰하였다.
또한 유리섬유 방진망에 전기방사 기술을 적용하여 제조된 샘플의 공기투과도는 자동 여과 성능 시험기(FX 3300 Labair IV)를 이용하여 측정하였으며, 동시에 분진포집효율을 평가하기 위해 TSI 8130A 자동 필터 테스트기(Automated Filter Tester 8130A)를 활용하여 분진포집효율(분진 입자 크기 0.3μm 기준)을 정밀하게 측정하였다.
4. 결과 및 토론
실험에 앞서 대중적으로 많이 사용하고 있는 유리섬유 방진망의 메쉬(18x16)를 목표로 실험하였다. 또한 전기방사를 수행하는 동안 테일러 콘과 제트의 형상을 육안으로 확인할 수 있었으며, 용액의 농도는 전기방사에 있어 섬유 형태와 직경 및 비드 변화에 큰 영향을 주기 때문에 매우 중요한 요인으로 꼽힌다. 이외의 다양한 매개변수 변화를 통해 PVDF 나노섬유를 관찰하고자, 유리섬유 방진망에 전기방사를 진행하였다.
가장 먼저 용액의 최적 농도를 확인하기 위해 전기방사 기술을 통해 수집된 부직포의 표면을 분석하였으며, Fig. 5.는 PVDF/DMF 용액의 농도를 각각 12, 15, 18wt%인 조건으로 전기방사를 진행해 얻은 FE-SEM 이미지이다. Fig. 5.와 같은 경우 PVDF/DMF의 용액은 점성이 높아 전반적인 구슬 형태의 비드와 불규칙한 섬유의 형태를 형성되는 것을 확인할 수 있다. 이러한 결과는 상대적으로 낮거나 높은 농도에서는 주사 팁 끝에 맺히는 용액의 흐름을 유지하기 힘들며, 표면장력을 극복하는데에 있어 한계가 있기 때문이다.
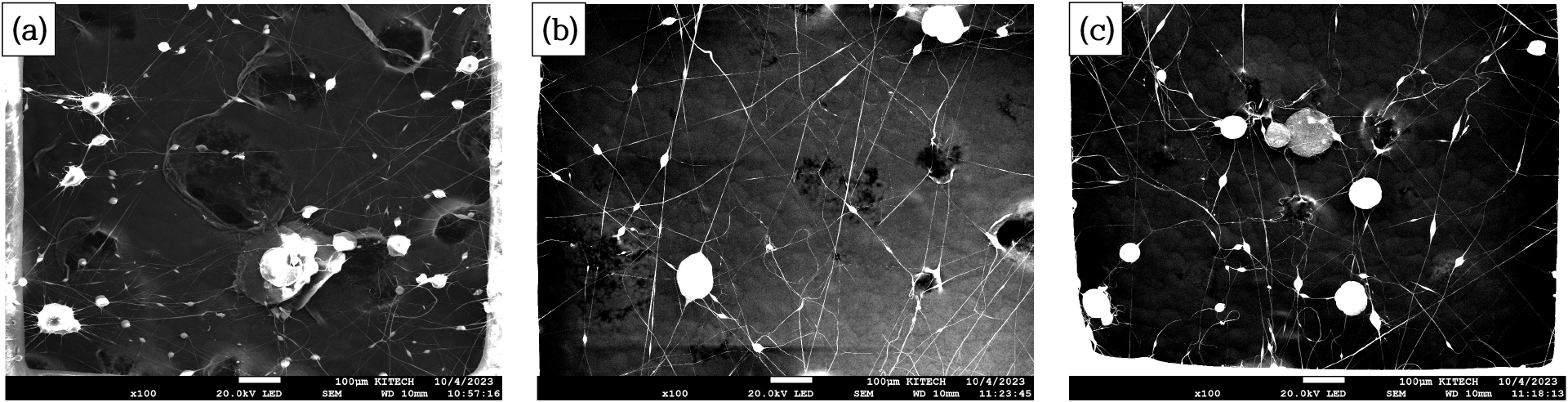
따라서 용매의 휘발성이 부족하다고 판단되었으며, 표면장력을 극복하고 섬유 형태와 비드를 더 세밀하게 관찰하기 위해 DMF보다 휘발성이 뛰어난 아세톤[8] 용매를 추가로 첨가하여 실험을 수행하였다. 용액의 농도는 Fig. 5.에서 전기방사 공정 중 육안으로 테일러 콘과 방출되는 제트의 형상은 유량이 증가할수록 안정적이며, PVDF 15wt%의 경우 눈에 띄게 인상적인 형상으로 관찰되므로 DMF와 아세톤의 질량비를 변화시켜 차이를 확인하였다.
Fig. 6.에 따르면 Fig. 5.에 비해 전반적으로 섬유 형태가 눈에 띄게 증가하였다. DMF/Acetone = 2:3인 (a) 경우 육안으로 관찰하여도 나노섬유 형태와 비드의 혼합이 이전과 유사하게 나타났다. DMF/Acetone = 1:1인 (b) 경우 FE-SEM을 통해서도 비드가 거의 관찰되지 않고 섬유 직경이 균일한 섬유를 확인할 수 있었다. DMF/Acetone = 3:2인 (c) 경우 섬유 형태와 비드의 혼합이 같이 관찰되었지만 섬유 직경이 조금 더 두꺼워진 나노섬유가 관찰되었다.
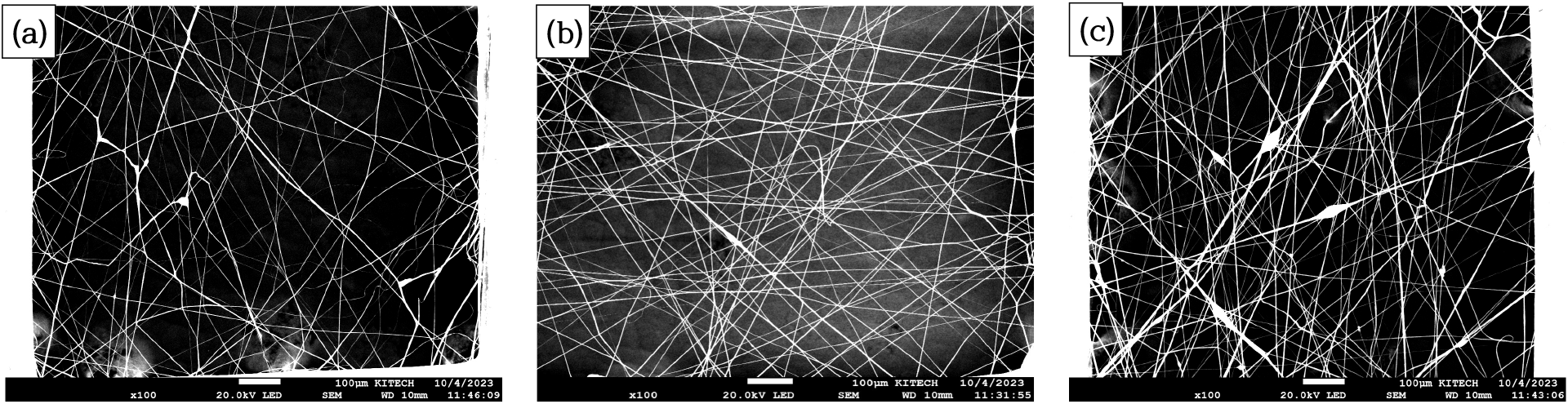
요약하면 Fig. 5.에서는 PVDF/DMF만을 사용하여 전기방사를 진행한 결과 섬유의 형태로 관측되기 어려웠으며, 중간중간 구슬 형태의 비드로 제작되는 것을 확인할 수 있었다. 반면에 아세톤을 첨가한 Fig. 6에서는 PVDF/DMF/Acetone 용액으로 인해 섬유 형성이 뚜렷하게 관측되었으며, 비드가 거의 사라지고 나노섬유의 균일함을 확인할 수 있었다.
따라서 아세톤의 첨가가 PVDF 용액을 통해 전기방사하는 과정에서 섬유의 형태 및 비드 생성에 긍정적인 영향을 미치는 것을 확인하였으며, 제조 과정에서 섬유의 두께를 균일하게 제조되도록 하여 섬유 품질을 향상시킬 수 있음을 확인하였다. 아세톤 비율이 증가함에 따라 제트가 방출되면서 증발하는 속도가 매우 빠르기 때문에 PVDF 용액이 빠르게 응고됨과 제트의 형상 반경이 작아짐을 확인하였다.
이에 아세톤을 첨가한 PVDF 용액의 질량비 1:1을 기준으로 방출 속도와 유량을 조절해 Fig. 7과 같이 섬유 직경을 나타내었다. 5.0 ml/h (a)에 경우 섬유 직경 0.6㎚~1.6μm과 같은 다소 얇은 섬유 직경을 가지지만, 약간의 비드도 함께 확인되었다. 8.0 ml/h (b)인 경우 1.3μm~2.0μm로 비드 없는 가장 균일한 나노섬유를 확인하였다. 10.0 ml/h (c)인 경우 1.7μm~3.0μm으로 가장 두꺼운 섬유를 형성할 수 있었다.
결과적으로 방사되는 용액의 양이 증가하면서 용매가 충분히 휘발되는 시간을 갖지 못하고 방출되는 용액이 튀면서 서로 뭉쳐 비드를 형성하게 되며, 육안으로 확인할 수 있는 테일러 콘과 제트의 형상에도 불안정하게 되는 영향을 미쳤다. 또한 유량이 증가함에 따라 니들팁 끝에 맺히는 용액의 양이 증가하여 섬유 직경이 두꺼워지는 현상을 확인할 수 있었다.
공기투과도와 분진포집율을 측정하기에 앞서 측정할 PVDF 용액은 Fig. 7.에 사용한 DMF/아세톤 질량비 1:1, PVDF 15wt% 용액을 선정하였다. 유량 차이와 방사 시간에 따라 방진망 섬유층이 얇거나 두꺼지며, 이에 따라 적절하게 조절하여 확인하고자 한다.
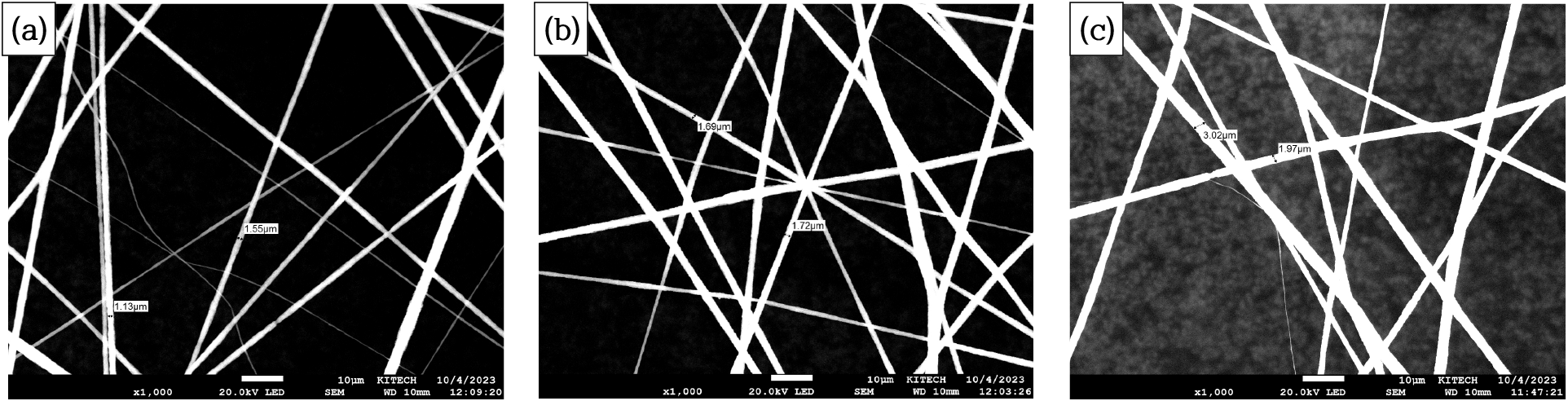
Table 1.과 같이 3분 전기방사 후 제조된 섬유의 공기투과도 측정 결과, 유량이 증가함에 따라 포집효율은 상승하지만, 이에 따라 공기투과도는 크게 감소하는 것을 확인하였다. 이를 개선하기 위해 Table 2.와 같이 방사 시간을 1분으로 줄여 재측정한 결과, 확연한 차이를 확인할 수 있었다. 측정 결과의 오차를 확인해 보기 위해 5회의 재측정을 시행하였을 때, Table 3.과 같은 오차범위와 신뢰할 수 있는 데이터를 확인할 수 있었다.
유량(㎖/h) | 공기투과도(mm/s) | 0.3㎛ 포집효율(%) |
---|---|---|
5.0 | 2265.68 | 7.85 |
8.0 | 1493.52 | 13.33 |
10.0 | 1092.20 | 15.51 |
유량(㎖/h) | 공기투과도(mm/s) | 0.3㎛ 포집효율(%) |
---|---|---|
5.0 | 6451.60 | 5.11 |
8.0 | 5130.80 | 6.57 |
10.0 | 4211.32 | 7.71 |
결과적으로 적절한 공기투과도와 분진포집율을 동시에 만족하는 샘플을 제조할 수 있었으며, 전기방사 기술을 적용한PVDF 미세먼지 방진망의 대한 특성에 대해 평가할 수 있다.
5. 결 론
본 연구에서는 실내 공기질을 효과적으로 개선하기 위해 PVDF 미세먼지 방진망을 연구하였다. 전기방사를 수행하는 동안, 우리는 다양한 매개변수를 조절함으로써 전기방사 최적 공정 변수를 확립할 수 있었으며, 특히, PVDF 15wt% 농도에서 가장 균일하며 비드가 없는 최적의 섬유 형태를 관찰할 수 있었다. 이 외에도 다양한 매개변수를 변화시킴으로써 PVDF 전기방사 나노섬유의 형성 및 특성을 관찰하고 연구할 수 있었다.
또한 이 연구를 통해 제조한 PVDF 전기방사 미세먼지 방진망은 기존 유리섬유 방진망에 대한 데이터와 비교해 보면, 기존 미세먼지 방진망은 공기투과도 7600mm/s, 0.3μm 분진포집효율 0.8%에 달했으나, PVDF 전기방사 미세먼지 방진망은 보시는 데이터와 같이 공기투과도와 포집효율 동시에 만족을 이루는 우수한 특성을 가지고 있음을 확인할 수 있었다.
비록 공기투과도의 자동 여과 성능 시험기는 7600mm/s의 수치를 초과하면 수치를 측정할 수 없었으며, 분진포집효율 같은 경우 분진 입자 크기가 0.3μm로 측정되었지만, 추후 실험에는 분진 입자 크기를 0~10μm인 경우 Table 4.과 같이 포집효율이 측정될 것으로 예상된다. 이는 미세먼지(PM10)부터 초미세먼지(PM2.5)까지도 효과적으로 제거할 수 있는 분진포집효율을 가진다. 따라서 이러한 성능 특성을 고려할 때, 기존의 유리섬유 방진망을 대체하는 용도로 활용할 수 있는 것으로 판단된다.
그러나 PVDF를 유리섬유 방진망에 전기방사 한 후 발생한 PVDF 섬유와 유리섬유 간의 접착력 문제는 향후 극복해야 할 과제로 엿볼 수 있다. 앞으로는 방진망 뿐만 아니라 다양한 분야에서의 응용 가능성이 더욱 기대되는 기술이며, 이에 따라 더 많은 전기방사 연구가 진행되어야 한다고 판단된다.