1. 서 론
신뢰성은 제품의 품질 속성에 관한 내용으로 1816년 Samuel Taylor Coleridge에 의해 처음 사용되었다.[1] 현재까지의 신뢰성은 부품의 신뢰도를 높이면 부품의 결합체인 제품의 신뢰도 또한 상승한다는 기본 이론으로 부품 신뢰도의 이론이 발전하였다. 기술의 발전과 더불어 시스템의 기능이 다양해지고, 이를 구성하는 하위 부품들은 소형화 되어 가면서 부품 간의 물리적 거리가 좁아져 부품 간의 상호작용성은 증가하였다.
제품의 신뢰성을 검증하기 위해서 부품 단위로 환경시험을 진행한다. 하지만 제품 단위에서는 부품 간 상호영향성에 대한 검증은 불가하였다. 신뢰성을 가장 중시하는 무기체계는 초기 기능의 동작 여부에 초점을 두고 개발하나, 점차 기능이 구현되더라도 전쟁 시에 사용하는 환경 특성상 특정한 조건과 시간에 고장이 발생하지 않고 정상적인 동작이 가능한지에 집중한다. 해외 선진 사례로 미국은 무기체계 개발 시에 신뢰성 설계는 부품이 조립된 이후 완성된 제품을 기준으로 시험하여 신뢰도를 성숙시키며 여러 시제품을 제작하여 신뢰성 시험을 진행한다. 특히, 군사 장비 중 하나인 함정 전투체계는 군의 운용 요구사항을 기술적 요구사항으로 분류하며, 분류된 기술적 요구사항들에 대해 요구사항에 적합한 기능 할당을 수행하여 그 결과로 기능에 부합하는 단위장비(부품 또는 모듈)를 선정 및 통합하여 체계를 설계한다. 따라서 단위장비 선정 시 사전에 실제 사용 환경에 문제가 없도록 설계를 진행하나, 단위장비 조립 후 환경시험을 수행하면 시험조건에 충족이 되지 않아 시험이 중단되는 사례가 환경시험 항목 기준 약 10%가 발생하고 있다. 환경시험의 실패 원인을 살펴보면 단위장비(부품 또는 모듈)의 사양은 시험조건에 부합하였다. 하지만 단위장비 간의 상호작용으로 인한 시험 실패가 약 70% 정도가 발생하였다. 또한 2000년대 초반 국내 함정 전투체계 개발을 시작한 이후 양산된 전투체계 A/S 기록 중 542건을 조사한 결과 상호작용(Interaction Failure)에 의한 고장으로 확인되었다. 상호작용 중에서도 시스템 상호작용(System Interaction)에 의한 제품 고장이 약 50%를 차지했다. 따라서 설계 초기 단계서부터 부품간 상호작용을 고려한 신뢰성 설계가 필요함을 선행 조사를 통해 알 수 있다. 기존의 설계 방법인 TAAF(Test, Analyze and Fix)는 제품을 만든 이후 시험을 통해 문제점을 발견하고 개선하여 제품을 다시 만드는 방법이다. 이는 제품에 대한 문제점을 식별하고 분석하는 장점이 있지만 비용과 시간이 많이 소요된다는 단점이 있다. 이에 기존의 설계 방법을 탈피한 효율적인 설계와 동시에 제품의 신뢰성을 높이기 위한 추가적인 방안이 필요하였다. 따라서 본 연구에서는 무기체계를 구성하는 장비 설계 시 신뢰성과 효율성을 동시에 높이기 위한 레고블록형 설계 방법과 상호작용 영향도 시험 방안을 제안하였다. 또한 실제 함정 무기체계에 탑재되는 전투체계의 적용 사례를 바탕으로 본 연구에서 제안한 레고블록형 설계와 상호작용 영향도 시험의 무기체계 개발 및 운용 간 적용 가능성을 검증하였다.
2. 레고블록형 설계 방안
레고블록형 설계를 위해 블록 단위를 설정하였다. 제안한 레고블록과 기존의 모듈화의 차이점은 아래 <Table 1>과 같다.
모듈형은 비슷한 시스템에서 재사용이 가능하도록 설계하며 레고블록형 설계는 타 시스템에서도 사용할 수 있도록 설계하였다. 시험방법도 기존 모듈형은 품질시험으로 성공과 실패로만 구분하였으나, 레고블록은 한계시험을 진행하기 때문에 어떠한 환경에서 문제가 발생하고 다른 레고블록에 영향을 주는지에 대한 정보가 기록된다. 이 정보는 장비의 예측 데이터로 활용이 가능하다. 모듈형과 레고블록형의 차이를 보면 시험 시기에도 차이가 발생하는데 모듈형 제품의 시험은 모듈이 조립된 상황에서 환경시험을 진행하게 되고 환경시험 중 발생한 문제의 원인을 규명하기에도 어려움이 있었다. 그러나 레고블록형 설계 시 레고블록에 대한 부품을 선정할 때 레고블록 단위 한계시험을 통해 실제 제품이 조립된 이후에도 발생이 가능한 고장을 예상할 수 있다. 이와 반면에 다른 결과가 도출되었을 때는 기존의 모듈형과 비교하여 레고블록형 데이터를 통해 고장 원인 파악이 수월하다.
블록 단위 설계 시 고려해야 할 사항 중 하나는 신호 흐름이다. 대표적인 사례로 <그림 1>의 함포 연동은 레이다로부터 수신된 표적을 가지고 자함 정보를 근거로 탄도 계산을 통해 예측하고 예측된 내용을 바탕으로 함포를 발사한다. BCU-Monitor 내용은 전투체계의 특성상 장비의 동작 여부를 측정하기 위해 감시 장치가 별도로 장착된다. OSD-ICU의 경우에는 수신된 자함의 정보를 전투체계 내부로 연동하는 장비이나 무장의 경우 전투체계 생존 여부와 상관없이 교전을 수행하기 위해 데이터를 연동 단으로부터 직접 수신하게 된다. 아래 <그림 2>의 내용은 함포 발사 절차에 관한 내용을 레이다로부터 표적을 획득한 이후로부터의 절차를 표현하였다. 다기능 콘솔의 운용자가 다기능 콘솔을 통해 함포의 상태 확인 명령을 요청하게 되면 랜스위치를 거쳐 BCU-SBC로 명령이 전달되고 BCU-ICU는 BCU-RS422 카드를 통해 연동하는 함포에 연동 확인 메시지를 전달하게 된다. 확인된 메시지는 다기능 콘솔을 통해 운용자에게 전달되며 운용자는 함포 발사 준비 명령을 하게 되고 이전의 절차와 동일하게 함포에 전달되어 피드백으로 함포가 발사 준비가 되었다면 상태 메시지를 전달하게 된다.
전달된 메시지는 다기능 콘솔을 통해 전시, 운용자는 함포 발사 명령을 내리게 되며 이전과 동일한 절차로 함포로 전달되어 발사 명령으로 함포가 발사된다. 함포 발사의 절차를 보면 단순히 하나의 정보를 전달하는 것이 아니라 명령과 상태값이 계속 변화하는 것을 알 수 있다.
레고블록의 블록 단위 선정에 대한 효율성 확인을 위해 설계구조 매트릭스 방법을 이용해 클러스터링하고 결과를 도출하는데 함정 전투체계의 경우 현재 모듈화가 되었다는 가정하에 현재의 모듈에 대한 효율성 측정을 진행하였다. <그림 3>은 무장 부분의 설계구조 매트릭스이다. 연동이 복잡하여 그 중에 일부인 무장 부분에 관한 내용을 사용하였다. 또한 LAN Switch의 경우 모든 데이터의 경로 역할을 하므로 설계구조 매트릭스의 클러스터링은 진행하지 않았다. 완료된 설계구조 매트릭스를 이용해서 효율성을 계산하면 아래와 같다. 여기서, N1은 대각 행렬(모듈)의 총 X(연관)수, N2는 대각 행렬(모듈)의 총 빈칸(Void)수, N3은 비대각 행렬의 총 X(연관)수, N4는 대각 행렬과 비대각 행렬의 총 X(연관)수 이다.
그룹화 측정 공식인 식(1)을 통해 함정 전투체계 중 BCU 장비에 대한 그룹화는 64%임을 확인하였다. 또한, 다른 형태의 그룹화 측정 공식인 식(2)를 통해 대각 행렬의 빈 공간과 대각선 행렬의 에외적 요소를 고려한 자중평균과 얼마나 컴팩트한지 측정해보았다. 그 결과 그룹화는 86%임을 확인할 수 있었다.
그룹화 공정능력 지수인 GCI(Grouping Capability Index)는 상호의존적인 요소 및 모듈 그룹에 대한 측정이며 식(3)을 통해 그룹화 효율성을 측정하였다. 그 결과 공정능력 지수는 86%임을 확인할 수 있었다.
활용률(Utilization)은 모듈에 대한 활용도를 측정하는데 사용하며, 식(4)를 통해 활용률을 측정하였다. 그 결과 활용률은 85%임을 확인할 수 있었다.
본 결과로부터 모듈화의 수준에 대한 그룹화(μ)와 효율성(η)은 각각 64.28%와 86.17%로 상당히 양호한 것을 확인하였다. 또한 BCU 모듈은 그룹화 능력지수(GCI)와 활용도(U)도 86.66%와 85.71%로 모듈형 설계가 양호하다는 결과를 도출할 수 있었다,
3. 상호작용 영향도 시험
<표 2>는 본 연구에서 제안한 레고블록 상호작용 영향도 시험 항목과 기준이다. 레고블록에 대한 시험의 목적은 레고블록 간의 영향성 인자를 확인하기 위해 환경 인자들에 대한 레고블록 자체 동작 한계를 측정하고, 하나의 레고블록에서 타 레고블록에 영향을 미치는 요소를 확인하기 위한 시험이다.
그 이유는 모듈화와 다르게 레고블록형 설계의 특징상 어떠한 환경요소에서 사용될지 모르는 상태에서 레고블록을 설계하기 때문에 레고블록의 특성에 대한 정보가 필요하다. 또한 레고블록의 자체 특성 확인 시 다른 레고블록에 미치는 영향에 대한 정보가 필요하다. 이는 레고블록을 단독으로 사용하는 경우보다 다른 레고블록과 함께 사용하는 경우가 다수이기 때문이다. 레고블록의 단독 시험에 대한 명칭을 본 연구에서는 IIO (Interaction In/Out Test) 시험으로 명명하기로 한다.
시험 항목에 대한 설계 인자는 기술적인 설계 방법, 통계적인 설계 방법, 경제적인 설계 방법이 있다.[2]~[17] 본 연구에서는 적용 사례 대상인 해군 함정 무기체계의 전투체계 특성상 5가지 항목에 대한 환경시험이 진행되므로 레고블록의 IIO 시험 항목은 현재 해군 전투체계 환경시험에서 진행하고 있는 5가지 시험 항목(온도, 습도, 진동, 충격 및 전자파)을 준용하였다.
시험조건은 시험 시 이루어지는 가혹도와 관련한 내용으로 일반적인 시험에서 가혹도를 결정하는 방법은 규격 비교 방법, 환경 조건을 이용하는 방법, 실험적인 방법, 데이터에 의한 분석적 방법이 있다. 레고블록 IIO 시험의 조건은 레고블록이 외부 환경으로부터 영향성과 타 레고블록에서 영향을 미치는 정도를 시험하기 위해서는 실험적 방법을 사용한다. 또한 레고블록의 가혹도 시험 시 중요한 사항은 아래 <그림 4>와 같이 파괴한계까지 시험하는 것이 데이터를 풍부하게 할 수 있으나 전투체계라는 특성으로 전투 시에 장비 동작 여부를 판단하는 요구 조건에 부합한 동작 한계까지의 데이터라면 IIO 시험의 취지에 부합한다. 또한 전투체계의 특성이 다품종 소량 생산이므로 제품의 단가도 높고 파괴시험 시에 시험에 소요되는 비용이
많아 동작 한계까지만 측정하였다. 레고블록의 IIO 시험 특성과 가혹도 설정의 실험적인 방법을 결합하여 초기 가혹도는 레고블록의 가용온도 조건을 시작 온도로 설정하며 동작 한계까지 가혹도를 증가시킨다. 주의해야 할 사항은 가혹도 증가는 파괴한계가 아닌 동작 한계까지이다.
시험조건 설정에서 레고블록형 설계의 특징상 <그림 5>와 같이 2가지 시험으로 구분이 필요하다. 레고블록이 외부로부터의 영향에 동작 한계를 측정하는 Interaction In 시험이고, 레고블록이 외부로 영향을 얼마나 주는지에 대한 Interaction Out 시험이 필요하다.
Interaction In 시험온도의 조건은 동작 한계까지 <그림 6>과 같이 계단형 스트레스 시험을 실시하게 되는데 단계별로 최대 10°C씩 증가시키며 레고블록의 사용 요구사항 이후에 온도 기준으로 5°C씩 증가시킨다. 온도 유지 시간은 10분이며 제품의 특성상 외부온도에 대한 안정화에 10분이 부족한 경우 추가적인 시험 설계도 가능하다.
Interaction Out 시험은 챔버로부터 온도를 설정한 이후 제품과 챔버가 온도 평형을 이룬 상태에서 챔버의 온도 유지장치 전원공급을 중단한 이후 10분간을 유지하며 온도를 측정하는 시험을 실시한다. 해당 시험의 목적은 레고블록이 환경의 변화에 따른 외부에 영향성 여부를 판단하는 데이터로 사용된다.
시험 시료는 사업의 특성을 반영하여야 하나 국제규격인 IECQ[18]에 의해 회원들의 합으로 시료 수를 제시하고 있다. 레고블록의 특성상 많은 곳에 사용을 위한 데이터로 시료의 수는 많을수록 좋으나 본 연구의 사례 대상인 사업이 8가지라는 특성과 함정 전투체계라는 특성을 고려하면 시료의 수는 1~3개의 시료로 적당하다고 판단하였다.
본 절에서는 부품 간의 상호작용 영향과 영향도 시험의 결과를 시각적으로 표현하는 방법을 제안하였다. 이를 설명하기 위해서 아래 <그림 7> 함정 무기체계에 탑재된 전투체계 중 함포에 관한 상호작용 영향도 시험 결과를 기준으로 설명하였다. 시험은 함정 전투체계가 환경시험 하는 항목인 온도, 습도, 진동, 충격 및 전자파 시험을 기준으로 설정하였다.
결과의 내용을 살펴보면 온도 부분에서는 내부의 탑재 모듈 중 운용온도가 가장 낮은 −5°C~50°C 상태로 유지할 수 있도록 모듈 통합 설계가 필요하며, 외부는 총열량의 합산이 690Kcal로 열 유동성 문제가 없는 것으로 판단된다. 습도 부분에서는 내부는 탑재 모듈 중 운용 습도가 가장 낮은 –98% 습도 상태로 유지할 수 있도록 모듈 통합이 필요하며, 외부는 시간당 총 3CC의 응축수가 발생할 수 있으므로 응축수가 흘러나갈 수 있는 드레인 홀 설계가 필요하다. 진동 부분 내부는 탑재 모듈 중 330~360Hz 진동에 취약점이 나타나며 공진 설계 시 취약 주파수 공진이 없도록 설계가 필요하였다. FAM 모듈에서 355Hz 공진점이 나타나 Single Board Computer에 영향이 있었다. 따라서 다른 공진점을 가진 FAN 제품 교체가 필요하다. 충격 부분 중 내부는 탑재 모듈 중 운용 충격량이 5.2G가 넘지 않도록 충격량 통합 설계가 필요하며, 외부는 외부로 충격에 대해 Shock Mount로부터 충격량이 6G가 전달되므로 Single Board Computer가 취약할 것으로 판단되어 전달 충격량을 줄이는 설계 또는 6G까지 견디는 Single Board Computer 제품변경이 필요하였다. 전자파는 내부로 탑재 모듈 중 100~115MHz의 전자파 동작에 문제가 발생하는 모듈이 있으므로 설계 시 주의가 필요하며, Single Board Computer에서 110MHz의 전자파가 발생하여 Synchro Card에 영향이 있을 것으로 판단되어, 장비 교체 또는 EMI 필터 설계를 통한 대책이 필요하였다.
상호작용 영향도 시험의 결과에 대한 직관적인 이해를 높이고 시각적인 표현의 적용 가능성을 확인하기 위해서 <그림 7> 상호작용 영향도 시험 결과를 <그림 8>과 같이 설계구조 매트릭스로 표현하였다. 모듈별로 서로 어떠한 부분에 영향을 주는지(+) 또는 영향을 감소시키는지(−)에 대한 표현이 가능함을 확인할 수 있었다.
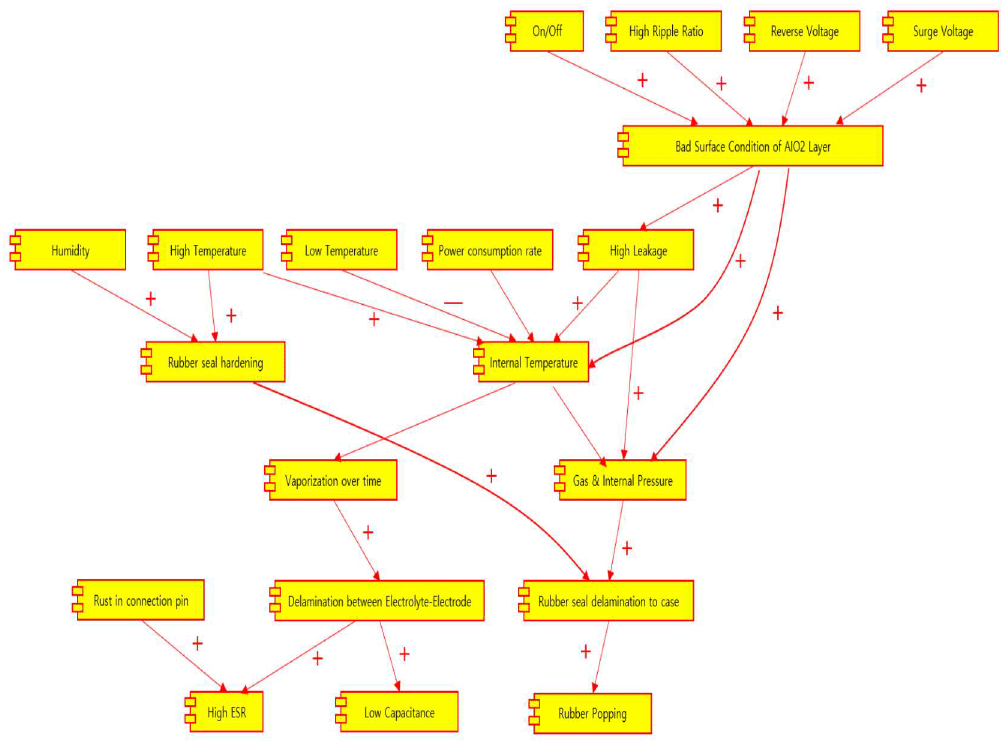
UML(Unified Modeling Language)은 시스템에 대한 개념 설계에 사용하기 위해 사용된다. <그림 6>과 같이 Component Diagram은 부품 간의 관계를 표현하는 다이어그램으로 사용된다. 고장의 영향성을 부품 간의 관계로 표현하게 되는데, 화살표와 +, − 기호를 통해 부품 간의 + 영향성과 − 영향성에 대해 시각적으로 표현이 가능하다.
이에 따라서 본 논문에서는 모듈별 상호작용의 영향성 확인을 위한 시각화 설계 방안을 제시하였다.
상호작용 시각화에 대한 개념은 상호작용 시험에 관한 결과에 대해 설계자에게 상호영향성을 시각적으로 인지시키는 방법이다. 레고블록형 설계를 기초로 고려한다면 위의 <그림 10>과 같이 표현된 상자이다. 제품인 상자 안에 레고블록이 탑재되는 형식을 고안하였으며, 각 레고블록은 상호작용 영향성 시험에 대한 항목으로 각 시험 항목에 대한 영향성을 다각형 모델로 표현하는 것이다. 따라서 하나의 제품에 레고블록 4개가 들어가고 5개의 상호작용 영향성 시험을 진행했다면 네모상자 안에 5각형 블록이 4개 들어간 형태를 보인다.
상호작용 영향성 시험의 항목이 5개인 경우 <그림 11>과 같이 5각형의 형태를 취하게 되며, 5개의 각은 각각 온도시험, 습도시험, 진동시험, 충격시험, 전자파 시험에 관한 내용으로 설정한다. 또한 각 형에 도넛 모양의 원이 작성되는 이는 영향성에 관한 내용으로 5각형 내부에 있는 부분은 상호영향성 내부 영향성 부분, 5각형 외부에 있는 부분은 외부 상호영향성을 나타낸다. 도넛 모양 중 띠 부분은 각 내부 영향성 시험 결과 중 취약한 부분 발생 시 띠로 표현이 가능하다. 또한 도넛을 통해 색상을 표시하여 이는 상대적인 취약성에 대한 평가 부분으로 가장 영향성이 적은 부분은 파란색 그보다 영향이 있으면 노란색, 노란색보다 더 영향에 민감하면 주황색 마지막으로 영향이 상대적으로 많은 부분은 적색으로 표시하게 된다.
위의 <표 2>의 내용을 상호작용 시각화를 통해 나타내면 <그림 12>와 같은 결과를 얻게 된다. 온도적인 면은 Synchro Card와 Power Supply, RS-422 카트, LAN Card 및 Single Board Computer에서 외부로 나온 열이 FAN의 외부로 발생한 진동 부분이 Single Board Computer에 들어가 Single Board Computer 내부 취약 부분에 영향을 준다는 내용을 화살표로 표현한 내용이다. 충격 부분을 보면 Shock Mount로부터 외부로 나온 충격이 Single Board Computer의 외부로 전자파가 나와 Synchro Card의 내부 취약 부분에 영향을 준다는 내용을 표현한 것이다. 본 논문의 해석이 달라질 수 있어 이에 대한 대안으로 시각화를 통해 설계 시 문제점을 바로 파악할 수 있는 다는 장점을 제공하기 위함이다. 따라서 레고블록 단위로 설계가 진행되고 레고블록 단위로 상호작용 영향성 시험의 결과 데이터를 상호작용 시각화를 통해 표현한다면 설계자에게 설계 과정에서 상호작용에 의한 고장을 예측할 수 있다.
4. 사례분석 및 검증
필드 데이터 분석은 실제 환경시험을 수행한 사례를 바탕으로 레고블록형 설계의 타당성을 확인하였다. 필드 데이터는 <그림 13>과 같이 총 8개의 실제 국방 연구개발 프로젝트에서 수행한 환경시험 결과를 사용하였다.
8개 프로젝트에서 수행한 환경시험은 고온시험(a), 저온시험(b), 습도시험(c), 전자파 시험(d), 진동시험(e), 충격시험(f), 수송시험(g), 함염안개 조건시험(h), 선체 운동 시험(i), 염수 분무 시험(j), 발포 충격시험(k)이며 각 프로젝트의 특성별로 환경시험 수행 여부가 다를 수 있다. <표 3>은 프로젝트별 수행한 시험 항목을 표시하였다. 8개 프로젝트 환경시험 계획 대비 실제 수행일을 아래 <그림 14>와 같이 비교하면 8개 프로젝트 전체의 환경시험 계획 일수는 917일이나 실제 환경시험을 수행한 일수는 1,044일로 약 13.8%의 추가적인 시험이 진행되었다. 이는 시험의 약 10% 이상이 환경시험 중 문제가 발생하여 재시험을 수행하였다. 또한 중요한 사안은 8개 프로젝트 모두 환경시험에서 문제가 발생하였다.
A | B | C | D | E | F | G | H | |
---|---|---|---|---|---|---|---|---|
a | ◯ | ◯ | ◯ | ◯ | ◯ | ◯ | ◯ | ◯ |
b | ◯ | ◯ | ◯ | ◯ | ◯ | ◯ | ◯ | ◯ |
c | ◯ | ◯ | ◯ | ◯ | ◯ | ◯ | ◯ | ◯ |
d | ◯ | ◯ | ◯ | ◯ | ||||
e | ◯ | ◯ | ◯ | ◯ | ◯ | |||
f | ◯ | ◯ | ◯ | |||||
g | ◯ | |||||||
h | ◯ | |||||||
i | ◯ | |||||||
j | ◯ | |||||||
k | ◯ |
환경시험은 전쟁 중 무기체계의 임무 수행 가능 여부를 확인하기 위해 설계되는데 단품으로는 문제가 없는 제품을 통합하여 하나의 장비로 만드는 경우 문제가 발생한다는 사실을 알 수 있다. 또한 <그림 15>와 같이 8개 프로젝트에서 장비별 시험 항목을 모두 합쳐 총 160개 시험 항목(온도, 습도, 진동, 충격, 전자파 등) 중 23건의 실패가 발생하였으므로 평균 14%의 실패 건수가 발생했다는 사실이다. 다만, 하나의 프로젝트가 장비가 1가지이고 시험 항목이 온도시험, 습도시험, 진동시험, 충격시험, 염수분무시험, 전자파 시험으로 총 6가지인데, 시험 도중 습도 시험, 진동시험 및 전자파 시험에서 문제가 발생하여 장비의 항목별 시험 실패율이 50%에 이른다. 이는 장비가 1개가 통계적인 모수가 작아 일반적인 상황이 아니라고 판단된다.
환경시험 결과에 대한 영향성 원인 파악이 필요하다. 원인이 파악되면 원인에 대한 대책 수립이 가능하기 때문이다. 아래 <그림 16>의 내용은 환경시험 실패의 원인이다. 환경시험 영향 원인으로 분류된 자재선정의 미흡한 내용은 제품을 구성하는 부품 자재의 결함으로 환경시험에서 실패되었으며, 그 제품을 사용하게 된 원인은 제품 설계 시 제품 간의 상호영향성 혹은 환경시험 조건에 부합 여부 판단이 안되었다는 것이다. 그 예로는 습도 시험으로 인해 부품에 부식이 발생하여 실패한 경우이다.
외부 영향 설계 미흡을 살펴보면 제품 설계 시 고려하고 있었던 외부 영향에 대해 스트레스가 적을 것으로 판단하였으나, 실제 환경시험 시 고려되지 않은 스트레스로 인해 환경시험이 실패가 된 경우다. 진동시험 시 하드디스크에 스트레스가 전달되어 화면이 정지한 사례로 진동에 견디도록 하드디스크의 장착대를 변경하여 시험을 통과하였다. 과도한 외부 영향을 기존에 예상되었던 설계값 이상으로 외부로부터의 영향이 전달된 경우로 충격시험 시 충격이 내부로 전달되어 내부의 배터리가 탈착되어 환경시험에 실패한 경우다. 이 경우는 외부 영향 값에 대해 일차적으로 충격을 흡수하는 쇼크 마운트의 설계가 미흡하여 내부로 충격값이 전달된 사안으로 충격 흡수율을 높인 쇼크 마운트 설계로 수정하여 환경시험을 재수행하였다. 설치 영향에 대해 살펴보면 환경시험수행 시 시험수행을 위한 고정대를 제작하여 장비가 장착된 방향으로 설치를 하는데 환경시험 수행 중 설치대가 변형되어 시험에 실패한 사안이며 변형이 없도록 재제작하여 환경시험을 수행하였다. 검증 장비 미흡은 환경시험 진행 도중 환경시험 대상 장비의 동작 여부를 확인하기 위한 외부 장비로 특히 동작 고온/저온시험 시 장비 상태를 관찰한다. 그러나 장비 상태를 관찰하는 장비의 고장 발생 시 환경시험 대상 장비의 동작 유무 판단이 어려워 환경시험을 중단한 사례이며 관찰 장비를 교체하여 재시험을 수행한 사례이다. 그 외 사안으로 환경시험 중 예기치 못한 정전으로 인해 시험이 중단된 사례 그리고 환경시험이 진행 도중 고객의 요구사항 변경으로 제품의 설계가 변경되어 환경시험을 중단한 사례가 있었다.
환경시험 실패 원인에 대해 사전에 예측할 수 있는지 즉 레고블록형 설계 시 이루어져야 할 상호작용 영향도 시험 시 어떠한 변화가 있을지 예측해 보면 <그림 17>과 같이 자재 선정 미흡 부분과 영향성 설계 미흡 부분에 대해서는 상호작용 영향도 시험 항목인 습도 시험에서 충분히 확인할 수 있었다. 또한 영향성 설계 미흡의 경우 각 레고블록 단위의 상호작용 영향도 시험에 관한 결과로 상호작용 시각화하게 된다면 영향도도 사전에 파악할 수 있었다. 그 결과 상호작용 영향도 시험이 사전에 실시된다면 환경시험의 실패 원인의 56%를 사전에 예측할 수 있다.
환경시험 실패 원인과 상호작용에 대한 관계를 <그림 18>과 같이 살펴보면 환경시험의 실패 원인 중 68%가 부품과 부품 간의 상호작용에 의한 고장이라는 원인을 찾을 수 있었으며, 상호 작용에 의한 고장이 원인인 내용 중 상호작용 영향도 시험을 통해 예측할 수 있다고 판단되는 경우는 자재선정 미흡 분야 16%, 스트레스 영향성 부분 16%, 외부 영향 설계 미흡 20%, 과도한 외부영향 4%이다.
본 논문에서는 부품 또는 모듈 단독의 사양은 환경시험 조건에 부합하도록 부품을 선정하고 조합하여 제품을 제작하였으나, 환경시험 중 실패가 발생하였다. 그 원인을 살펴보면 부품 간 또는 모듈 간의 상호작용에 의한 고장이 많은 부분을 차지하고 있었다. 따라서 그에 대한 대책으로 레고블록형 설계 방법을 적용하여 블록 단위를 정의하고 블록 단위별로 상호작용 영향도 시험 즉, 블록 단위로 외부로부터의 영향에 대한 동작 한계를 측정하고, 또한 기능 수행을 위한 블록 동작 시 내부로부터 외부로 가해지는 영향성에 대한 측정을 수행하였다. 여기서 수행된 결과를 자료화하고 데이터는 상호작용 시각화 방법을 통해 블록 간의 조합 시 예측되는 상호작용에 대한 영향성 확인이 가능함을 확인할 수 있었다.
결과적으로 <그림 17>의 환경시험과 상호작용 원인 파악 결과와 같이 레고블록형 설계와 상호작용 영향도 시험을 진행하게 된다면 현재의 환경시험 수행 중 발생하는 상호작용에 의한 환경시험 실패에 대해 56%를 예측하고 예방할 수 있다. 장비의 신뢰도 측면에서 환경시험에 통과한 제품은 실제 야전에서 운용에 문제가 없는지도 고려해봐야 한다. 그 이유는 장비의 신뢰도는 환경시험이 주목적이 아니라 장비의 총 수명주기관리 차원에서의 관련된 이야기이기 때문이다.
<그림 19>의 내용은 함정 전투체계 장비 중 환경시험을 통과하여 실전 배치된 장비에 대해 최근까지 정비한 이력의 내용을 시각화한 자료이다. 이를 통해 시스템 간 상호작용에 의한 고장이 50%를 차지함을 알 수 있다. 장비가 환경시험이 완료되어도 실전에 배치되어 운용하게 되면 시스템 간의 상호작용으로 인한 문제가 절반을 차지한다는 것이다. 이는 지금까지 환경시험만으로도 야전 배치 이후 발생이 가능한 고장과 같은 문제를 모두 제거할 수 없다는 것을 증명한다.
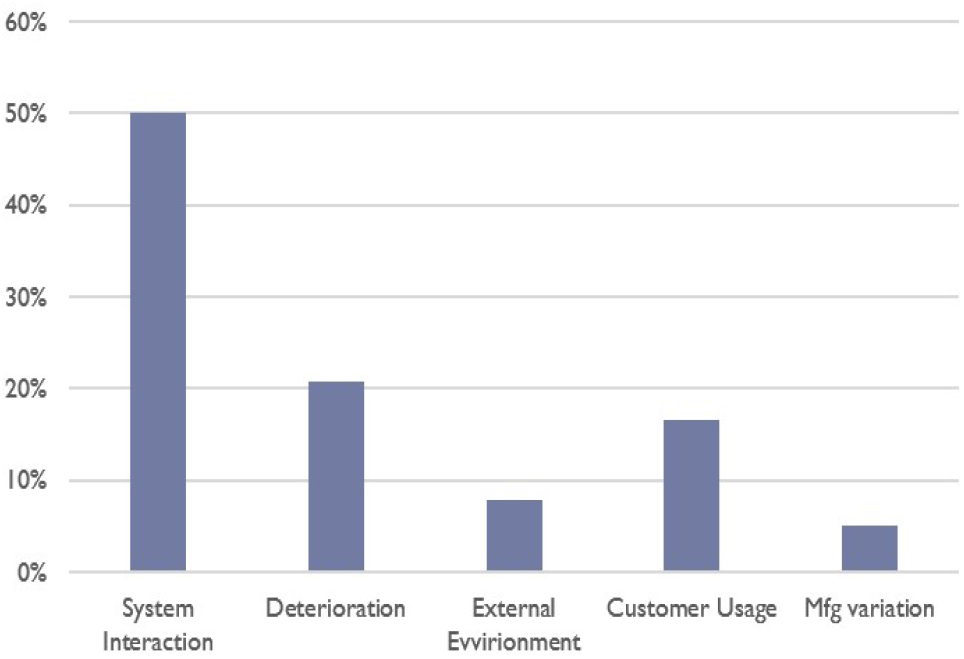
그 이유를 살펴보면 환경시험은 통과 시험 인증시험으로 특정한 환경에서 장비가 동작하는지에 관한 내용이며, 따라서 함정 간의 크기에 따른 파도 충격 전달량과 움직임이 설치된 위치에 따라 환경 조건이 다를 수 있으나 환경시험은 동일한 조건으로 진행되어 환경 특성이 반영되지 않기 때문이다. 야전 운용 제품 542건의 전체 정비현황에서 상호작용에 의한 고장으로 판단되는 268건의 원인을 살펴보면 <그림 20>과 같이 Display 정비 30%, PCB Board 정비 28%, Cable 정비 12%, Power 관련 정비 24%, 기타 6%로 집계되었다. 이 데이터는 Display, PCB Board, Power 관련 정비가 총 82% 부분을 차지하여 3가지가 대부분의 정비 내용을 차지한다. 여기서 중요한 사안은 82%에 달하는 3가지 부분은 모두 열원과 관련되어 있었다. 환경시험은 단기간으로 길어야 15일 정도 수행하여 열에 대한 축적적인 제품의 영향이 없으나 짧게는 몇 년, 길게는 10년 이상 된 장비들은 열 관련된 문제가 대부분을 차지하였다.
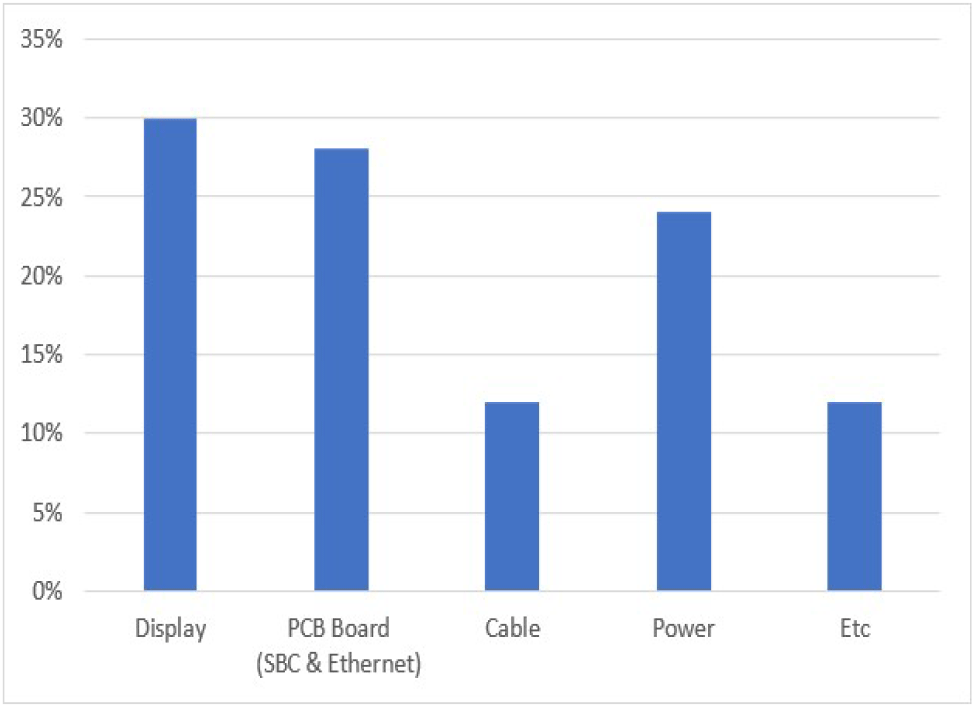
야전에서 운용 중인 장비의 정비 결과에 관한 내용 또한 상호작용 영향도 시험이 진행되어 블록별 동작 온도가 정확하게 파악되었다면 장비의 운용 환경 문제로 인한 제품의 결함인지 아니면 제품 자체의 문제인지 확인할 수 있으나 데이터가 없어 정확한 원인 파악이 불가하다. 따라서 레고블록으로 모듈을 분류하고 블록 단위의 상호작용 영향도 시험을 수행하게 된다면 제품을 운용하는 환경의 문제인지 제품의 문제인지 그리고 무엇보다 제품의 문제인 경우 다시 피드백되어 블록의 특성에 대한 추적이 가능하고 동일한 제품 사용 시 문제 부분에 대한 예상이 가능하다. 따라서 레고블록별로 상호작용 영향도 시험이 진행되고 블록별 정비 이력에 대한 추적이 이루어진다면 제품의 폐기 시까지 신뢰성 높은 장비 개발과 운용이 가능하다.
5. 결 론
본 논문에서는 무기체계를 구성하고 있는 하위 부품 간 상호작용에 의한 고장을 최소화하고 이를 식별하기 위한 방법으로 레고블록형 설계 방법을 제안하였다. 첫 번째는 레고블록 단위를 선정하고 블록 단위의 타당성 검증을 통해 블록 단위를 선정하였다. 레고블록의 단위를 정하는 문제는 그룹화 측정 공식[20], 그룹화 공정능력 지수[21], 그룹화 활용률[22]내용을 통해 블록 단위의 타당성을 확인하였다. 두 번째는 설정된 레고블록을 기준으로 상호작용 영향도 시험에 대해 정의하였다. 기존의 환경시험은 구성품 간 상호작용으로 인한 고장 예측이 불가하여 본 연구에서는 상호작용 영향도 시험을 제안하였다. 상호작용 영향도 시험은 외부 환경으로부터 레고블록 자체의 동작한계를 측정하여 블록의 한계 데이터를 측정하고 특정 레고블록의 동작 시 타 블록의 영향성이 있는 외부 발생 영향성에 대해 측정이 가능하다. 셋째는 측정된 레고블록 자체의 환경에 대한 동작한계 데이터와 레고블록의 동작 시 발생하는 외부로의 영향성에 대한 데이터를 바탕으로 상호작용 시각화를 수행하여 제품선정에 따른 상호작용에 의한 영향 확인이 가능함을 확인하였다. 이를 통해 본 연구에서 제안한 레고블록형 설계 방안을 적용하고 수행한 환경시험을 통해 실패 원인을 파악한 결과 기존 환경시험에서 56% 실패를 최소화 할 수 있음을 확인하였다. 또한 환경시험을 이미 수행한 장비는 야전에 배치한 이후의 고장 이력을 분석한 결과 50%가 상호작용이 고장의 원인임을 파악하여 환경시험 이후의 상호작용에 의한 고장도 예측이 가능할 것으로 파악되며, 이는 야전에서 수행되는 정비 소요 비용과 동시에 레고블록형 설계 방안이 야전에 배치된 무기체계의 신뢰도 향상에 기여함을 확인할 수 있었다. 향후 연구는 본 논문을 통해 도출된 상호작용 영향도 시험을 결과를 바탕으로 모델링의 정확도 향상 방안 연구가 필요하다.